University of New Mexico and Air Force Research Laboratory scientists have teamed up to prolong the life of solar modules by harnessing the Atom Ant-like strength of carbon nanotubes.
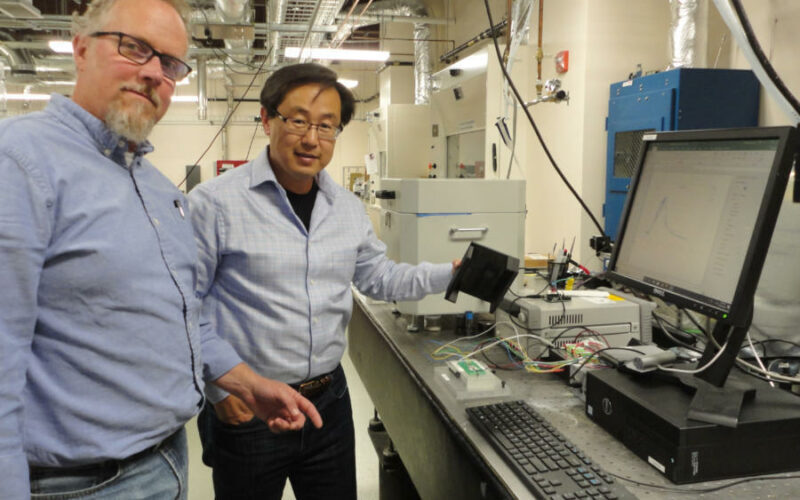
The scientists, Sang M. Han of UNM and David Wilt of AFRL in New Mexico, created a composite material that meshes carbon nanotubes with silver, the standard metal used to conduct electricity in solar cells and modules. They call it MetZilla, or Godzilla-infused metal, which they say could extend the life of solar panels to a minimum of 35 years, and potentially up to 50.
MetZilla, they say, can keep the metal conducting lines on solar cells intact even as the modules crack over time from extreme weather and other hazards. That could substantially lower the cost of solar cells and panels while boosting electric output from photovoltaic systems.
Cracking and cell degradation are chronic problems in solar systems, especially since the industry has moved to much thinner solar cells and modules to lower production and installation costs. As the panels get thinner, they become more vulnerable, making them more prone to degradation from the elements.
MetZilla’s potential to solve that problem attracted the New Mexico Angels, a group of about 70 individuals who pool their resources to invest in startups. The Angels launched Osazda Energy LLC in 2017 to take MetZilla to market through their Startup Factory, an incubator the Angels set up in 2012 to commercialize promising technologies developed at UNM and other state research universities.
“This is something that’s really needed in the PV market,” said Angels President and now Osazda CEO John Chavez. “The National Renewable Energy Laboratory has consistently listed this as the No.1 or No. 2 problem in the solar industry in recent years. If we can solve the problem of cracking and degradation, the market is ready, willing and able to adopt our product.”
The company received $1.5 million in grants this year to further develop and prove their technology from the Durable Module Materials Consortium, or DuraMAT, which groups the U.S. Department of Energy’s national laboratories, research universities and solar manufacturers together in an alliance to build new materials and designs for PV modules.
The company previously received a $150,000 Small Business Innovation Research grant from the Air Force, $50,000 in matching funds from the state Economic Development Department, and an undisclosed investment from the Angels.
It’s now doing robust laboratory testing to show how MetZilla-infused solar cells hold up against extreme temperature changes and pressure compared with cells with standard metal conducting lines, said Han, a UNM regents professor in both the Chemical and Biological Engineering and Electrical and Computer Engineering departments.
The goal is to keep electricity moving through the metal lines despite cracks on the solar cells, which tend to pull those lines apart over time. That disrupts electric flow and eventually interrupts it altogether as module degradation leads to open gaps in the lines.
“We introduce cracks into the solar cells and then we push them up and down with a plunger and submit them to thermal (hot and cold) cycling to see how the cracks progress over time with and without the MetZilla paste,” Han said. “We’re at the stage of minimodule qualification, not rooftop-size modules. We want to prove the technology out first at a smaller module scale.”
The tests have shown MetZilla can easily bridge conducting-line gaps caused by cracks in cells of up to 30 microns, and well above 70 microns in some cases, Han said.
Solar cells with standard metal lines generally separate with solar cell cracks of under 5 microns.
The key to MetZilla is the carbon nanotubes fused into the metal paste. The nanotubes are mechanically strong and have good electrical and thermal conductivity, said Wilt, a senior physicist and technical adviser for the Spacecraft Component Technology Branch of the AFRL’s Space Vehicles Directorate.
As the metal lines get stretched from cracking on the solar cells, MetZilla helps bridge those gaps, Wilt said. In addition, the carbon nanotubes help heal the gaps in the lines.
“MetZilla maintains electric flow because the carbon nanotubes seek each other out,” Wilt said. “They reconnect with each other in a self-healing process.”
Wilt first thought of injecting carbon nanotubes into metal conducting lines while working to resolve solar-cell cracking and module degradation in Air Force spacecraft. He sought Han’s help in 2012 to develop the technology, backed by a $180,000 internal AFRL grant that supported about three years of joint research that included some of Han’s students.
They patented the technology together through the Science and Technology Corp., UNM’s tech transfer office.
“It’s a joint project,” said STC President and CEO Lisa Kuuttila. “It’s led to the first company created based on joint research between UNM and the AFRL.”
Apart from industry, the technology could benefit U.S. defense agencies, said AFRL Technology Engagement Office Director Matthew Fetrow.
“The Air Force could be a customer for that technology,” Fetrow said. “There are both commercial and defense markets for it.”
The company has created two MetZilla products, the MetZilla paste for use in terrestrial solar systems, and a MetZilla plating technology for use in solar powered spacecraft.
The paste is used as an ink to lay down metal lines on solar cells with a standard screen printer. The plating technology is for more robust solar panels for spacecraft. It uses an electroplating process to deposit MetZilla-based conducting lines by dipping negatively charged solar cells into a liquid solution that contains positively charged MetZilla ions, which then attach to pre-designed line patterns on the cell.
The company aims to have its first products ready for market in about 18 months. It employs seven people at two offices at UNM’s Science and Technology Park, and at the Sandia Science and Technology Park. Hans conducts lab work at UNM.